The Role of High-Quality Metal Fittings in Successful Shutdowns
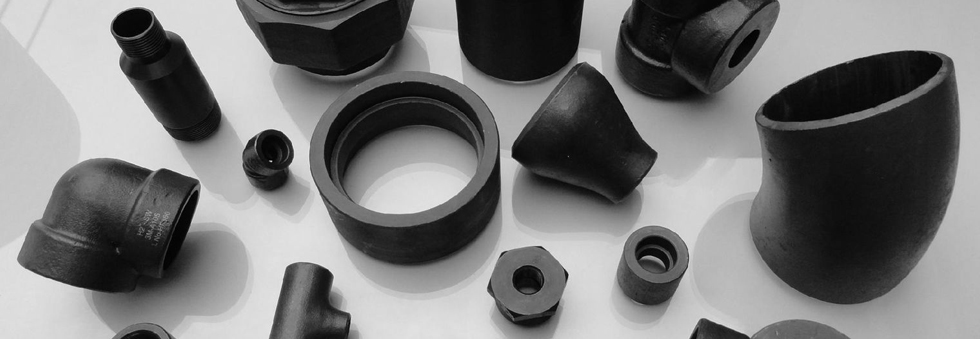
Plant shutdowns are an integral part of industrial operations, providing the necessary time for maintenance, repairs, and upgrades. While these planned interruptions can be costly, they are essential for ensuring the long-term safety and efficiency of equipment. A critical factor that contributes to the success of these shutdowns is the use of high-quality metal fittings. This article explores the importance of these components and how they help streamline shutdown processes.
Why Metal Fittings Matter in Industrial Operations
Metal fittings, including nuts, bolts, washers, and pipe fittings, play a pivotal role in holding various components together. They ensure that machinery and equipment function correctly by providing secure connections that withstand pressure, vibration, and other operational stresses. During shutdowns, these fittings are often inspected, repaired, or replaced to guarantee optimal performance when the plant resumes operations.
Key Benefits of High-Quality Metal Fittings
1. Enhanced Safety
Safety is a top priority during plant shutdowns. High-quality metal fittings contribute to safe operations by reducing the risk of equipment failure. Poorly made or worn-out fittings can lead to leaks, breakages, and other hazards that can endanger workers and the facility.
Using durable, corrosion-resistant fittings ensures that connections remain secure, minimizing the risk of accidents and ensuring that equipment can be restarted safely after maintenance.
2. Durability and Reliability
Industrial equipment is subject to extreme conditions, including high temperatures, pressure, and corrosive substances. High-quality metal fittings are engineered to endure these harsh environments without deteriorating quickly.
Investing in robust fittings means fewer replacements and repairs in the long term, leading to less frequent shutdowns and reduced maintenance costs.
3. Efficiency During Maintenance
During shutdowns, every minute counts. High-quality metal fittings simplify maintenance tasks, making it easier for technicians to disassemble and reassemble equipment. This efficiency is crucial for reducing downtime and completing shutdowns on schedule.
Reliable fittings also ensure that equipment can be reassembled without complications, allowing for smooth, hassle-free restarts.
4. Corrosion Resistance
Corrosion is a common issue in industrial environments, especially in plants dealing with chemicals, water, or high humidity. Over time, corrosion can weaken metal fittings, causing leaks or structural failures.
High-quality fittings are often made from materials that resist corrosion, such as stainless steel or brass. This resistance extends the lifespan of the fittings, ensuring long-term reliability and safety.
5. Cost-Effectiveness
Although high-quality metal fittings may have a higher upfront cost, they offer cost savings in the long run. Their durability reduces the need for frequent replacements, saving on both parts and labor costs.
Additionally, the reduced risk of equipment failure can prevent costly repairs and production downtime, further justifying the investment in superior fittings.
Types of High-Quality Metal Fittings for Shutdowns
1. Bolts, Nuts, and Washers
These are the basic yet vital components that hold machinery parts together. High-grade versions are made from materials like stainless steel, alloy steel, or nickel alloys to ensure strength and resistance to wear.
2. Pipe Fittings and Flanges
These fittings are essential for connecting pipes in fluid systems. High-quality fittings ensure leak-proof connections, which is crucial for systems carrying hazardous or high-pressure fluids.
Best Practices for Using Metal Fittings During Shutdowns
1. Conduct a Thorough Inspection
Before starting maintenance, inspect all fittings for signs of wear, corrosion, or damage. Replace any fittings that do not meet safety standards.
2. Choose the Right Materials
Select fittings made from materials that are suitable for the specific operational conditions of your plant. For example, stainless steel may be ideal for high-corrosion environments, while brass can be used for fittings in systems requiring excellent conductivity and heat resistance.
3. Partner with Reliable Suppliers
Working with a reputable supplier ensures that you receive consistent, high-quality fittings that meet industry standards. This reliability is critical for preventing unexpected issues during shutdowns.
4. Keep an Inventory of Essential Fittings
Maintaining a stock of critical metal fittings helps avoid delays during maintenance. It allows technicians to quickly replace parts without waiting for new supplies, ensuring that the shutdown process runs smoothly.
High-quality metal fittings are more than just small components; they are essential for the safety, efficiency, and reliability of industrial plants. During shutdowns, their role becomes even more critical as they facilitate maintenance and ensure that equipment can resume operations without issues. By investing in superior fittings and adopting best practices for their use, plants can minimize downtime, reduce maintenance costs, and maintain safe, smooth operations.
The right metal fittings are a vital part of successful shutdowns. Their durability, safety features, and resistance to harsh conditions make them an indispensable element of any industrial maintenance strategy.