The Role of Carbon Steel Fittings in Industrial Shutdowns and Turnarounds
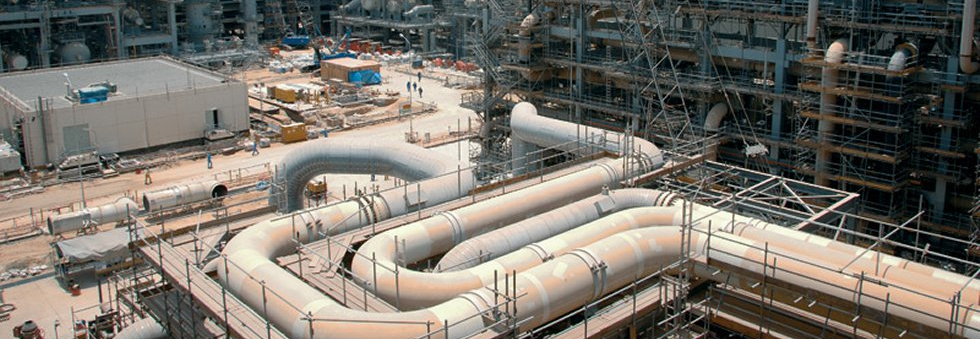
The Role of Carbon Steel Fittings in Industrial Shutdowns and Turnarounds
In industries like oil and gas, power generation, petrochemical, and manufacturing, scheduled shutdowns and turnarounds are critical for maintaining the efficiency and safety of operations. These events involve the inspection, repair, and replacement of essential components, and one of the most important materials used in these processes is carbon steel fittings.
Carbon steel fittings—such as elbows, tees, reducers, couplings, and caps—play a vital role in maintaining the integrity and safety of piping systems during shutdowns and turnarounds. In this blog, we’ll discuss the significance of these fittings, their benefits, and why they are indispensable for industrial maintenance.
What Are Carbon Steel Fittings?
Carbon steel fittings are components used to connect, redirect, or close off sections of piping systems. These fittings are made from carbon steel, a strong and durable material composed primarily of iron and carbon. The carbon content increases the steel’s hardness and strength, making it an ideal choice for high-pressure, high-temperature applications.
Why Carbon Steel Fittings Are Essential for Industrial Turnarounds
1. Durability in Extreme Conditions
Many industrial processes expose piping systems to extreme temperatures, pressures, and corrosive substances. Carbon steel is known for its high strength and ability to withstand these harsh environments. This makes carbon steel fittings ideal for use in power plants, chemical refineries, and oil rigs where durability and resilience are crucial.
2. High Strength and Pressure Resistance
Piping systems in industrial plants often carry liquids or gases at high pressures. Carbon steel fittings can handle these high-pressure environments without warping or failing. This ability to endure heavy loads and pressures makes carbon steel fittings essential for maintaining the structural integrity of piping systems during critical shutdown repairs.
3. Cost-Effectiveness
Compared to stainless steel and other alloy materials, carbon steel is significantly more affordable. For industries facing frequent maintenance cycles, using carbon steel fittings helps reduce costs without sacrificing quality or performance. This affordability makes carbon steel fittings a practical solution for both small and large-scale turnarounds.
4. Corrosion Resistance (with Coatings)
While carbon steel is not as naturally corrosion-resistant as stainless steel, it can be coated or treated with anti-corrosion substances. This treatment helps extend the life of carbon steel fittings, ensuring they last longer in corrosive environments such as chemical plants or offshore oil platforms.
5. Versatility and Availability
Carbon steel fittings come in various shapes and sizes, including elbows, tees, couplings, and reducers. Their availability in a wide range of configurations makes it easy for maintenance teams to find the right fitting for specific repairs or replacements during shutdowns. The versatility of carbon steel fittings allows them to be used in various applications, from connecting pipes to changing flow directions or reducing pressure.
Common Applications of Carbon Steel Fittings During Turnarounds
a. Pipeline Repairs and Modifications
One of the primary reasons for shutdowns is to repair or modify existing pipelines. Carbon steel fittings such as elbows and tees are used to redirect flow, while couplings and unions allow for easy connection between pipes. These fittings ensure that repairs are completed efficiently, minimizing downtime.
b. Pressure Vessel Maintenance
Carbon steel fittings are also used in pressure vessels, which are crucial components in many industrial processes. These fittings allow for the safe connection of pipes to the vessel, ensuring that high-pressure operations can resume without leaks or failures.
c. Boiler and Heat Exchanger Repairs
In industries like power generation and refineries, boilers and heat exchangers play critical roles. Carbon steel fittings help maintain these systems by ensuring that fluid flows are properly managed and that systems are reassembled securely after repairs or inspections.
Key Carbon Steel Fittings for Shutdowns and Turnarounds
1. Elbows
Elbows are used to change the direction of flow within a piping system. Carbon steel elbows are especially useful in industrial applications that require high-pressure resistance and durability during turnarounds.
2. Tees
Tees are used to connect three sections of pipe, allowing fluids to flow in different directions. They are essential when rerouting or modifying piping systems during shutdowns.
3. Reducers
Reducers allow for the connection of pipes with different diameters, ensuring smooth flow transitions between systems of varying sizes. They are commonly used in shutdowns when upgrading or replacing parts of a piping system.
4. Couplings
Couplings are used to connect two pieces of pipe securely. These fittings are crucial for creating leak-proof connections during shutdown repairs.
Industrial shutdowns and turnarounds are complex processes that demand the use of high-quality, durable materials to ensure safe and efficient maintenance. Carbon steel fittings provide the strength, durability, and cost-effectiveness needed to withstand the pressures and stresses of industrial operations. From repairing pipelines to maintaining boilers, carbon steel fittings play a crucial role in ensuring that systems are restored to full operational capacity after a shutdown.
Choosing the right carbon steel fittings during your next turnaround project can significantly reduce downtime, prevent future breakdowns, and enhance the overall safety and efficiency of your operations.